Discover how advanced fuel tracking technologies can revolutionize your logistics operations, reduce costs, and enhance sustainability.
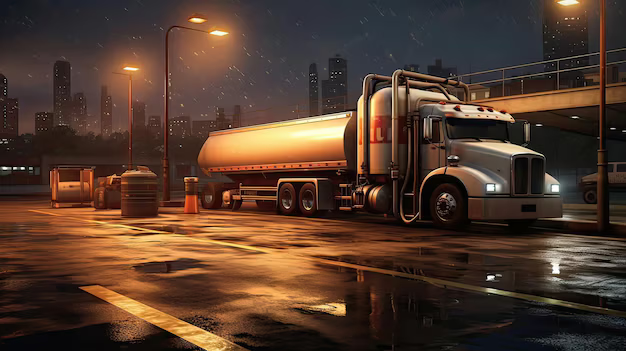
Introduction
In the fiercely competitive world of trucking and logistics, fuel expenses often account for 30-40% of total operational costs. Managing fuel efficiently isn't just a matter of cutting expenses; it's a strategic imperative that can significantly boost your company's profitability and sustainability. By implementing advanced fuel management solutions and integrating them with your Enterprise Resource Planning (ERP) system, you can gain unparalleled control over fuel usage, leading to measurable savings and operational excellence.
This comprehensive guide delves into the intricacies of fuel tracking, exploring cutting-edge technologies and strategies that can transform your logistics operations. Whether you're grappling with fuel theft, inefficient routes, or compliance issues, this article provides actionable insights to help you optimize fuel management.
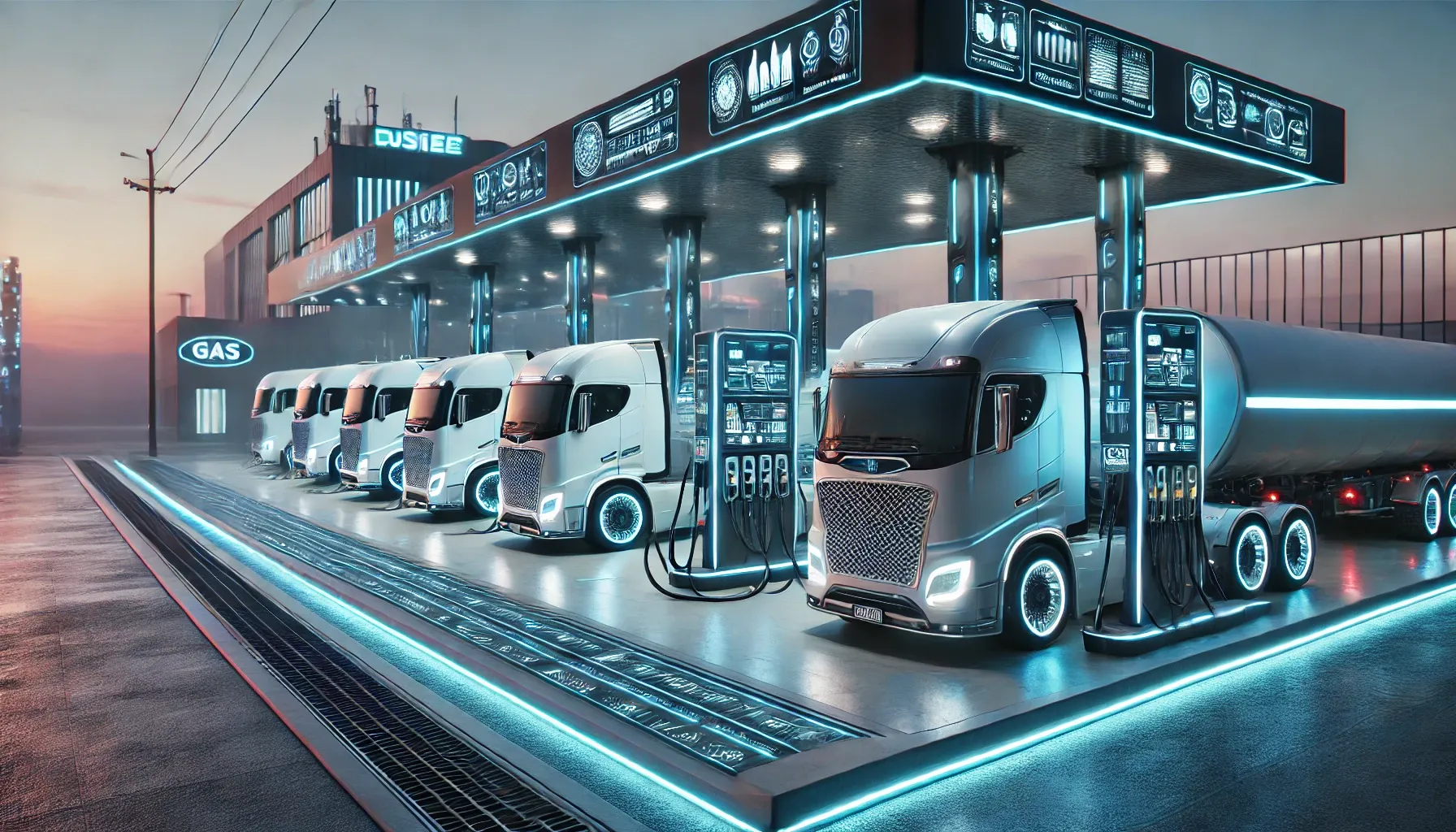
Why Fuel Tracking Matters in Logistics
Effective fuel tracking goes beyond mere monitoring of consumption; it's about leveraging data to drive strategic decisions that impact your bottom line. Here's why it matters:
- Reducing Operational Costs: By identifying inefficiencies and patterns in fuel usage, you can implement targeted measures to lower expenses.
- Preventing Fuel Theft: Advanced tracking systems can detect unauthorized usage promptly, safeguarding your assets.
- Enhancing Fleet Efficiency: Optimizing routes and encouraging better driver behavior can lead to significant fuel savings.
- Supporting Sustainability Goals: Reducing fuel consumption lowers carbon emissions, aligning your operations with environmental objectives.
- Ensuring Compliance: Maintaining accurate records is essential for meeting regulatory requirements and avoiding penalties.
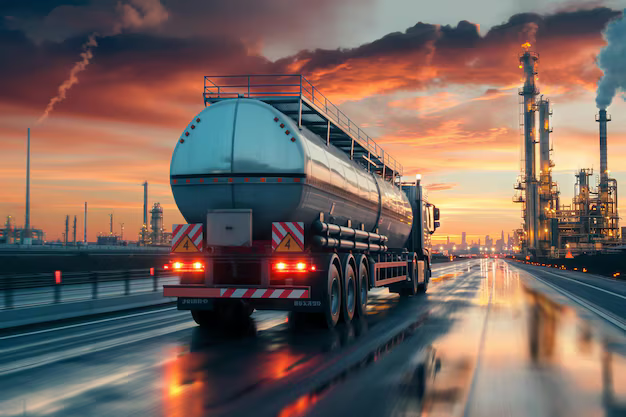
Challenges in Traditional Fuel Management
Manual Tracking Errors
Traditional fuel management often relies on manual data entry, leading to:
- Inconsistent Data: Human errors can result in inaccurate recording of fuel transactions, making it difficult to assess true consumption.
- Delayed Reporting: Consolidating data manually is time-consuming, delaying critical decision-making.
- Limited Visibility: Without real-time information, identifying issues or opportunities becomes a challenge.
Lack of Real-Time Data
The absence of immediate data access leads to:
- Delayed Decision-Making: Inability to respond promptly to anomalies such as sudden spikes in fuel usage.
- Inefficient Operations: Missed opportunities to optimize routes or address driver behavior.
- Increased Costs: Undetected issues can escalate, leading to higher expenses.
Inability to Detect Anomalies
Without sophisticated tracking:
- Fuel Theft: Unauthorized fueling may go unnoticed, resulting in significant losses.
- Mechanical Issues: Problems affecting fuel efficiency remain undetected, compromising vehicle performance.
- Uncontrolled Expenses: Rising costs occur without clear explanations, hindering financial planning.
Integration Issues
Disparate systems create silos:
- Data Silos: Disconnected systems make data consolidation challenging, preventing a unified view of operations.
- Workflow Inefficiencies: Automation in billing and inventory management is hindered, increasing administrative overhead.
- Limited Insights: Strategic decision-making is compromised due to fragmented information.
Advanced Fuel Tracking Technologies
Connected Fuel Pumps and Tanks
Veeder-Root and Piusi offer state-of-the-art connected fuel pumps and tank monitoring systems that revolutionize fuel management.
- Real-Time Monitoring: Gain instant access to data on every liter dispensed, enabling timely insights.
- Anomaly Detection: Receive alerts for irregular fuel usage, allowing prompt investigation and action.
- Secure Access: Prevent unauthorized fueling through advanced security features.
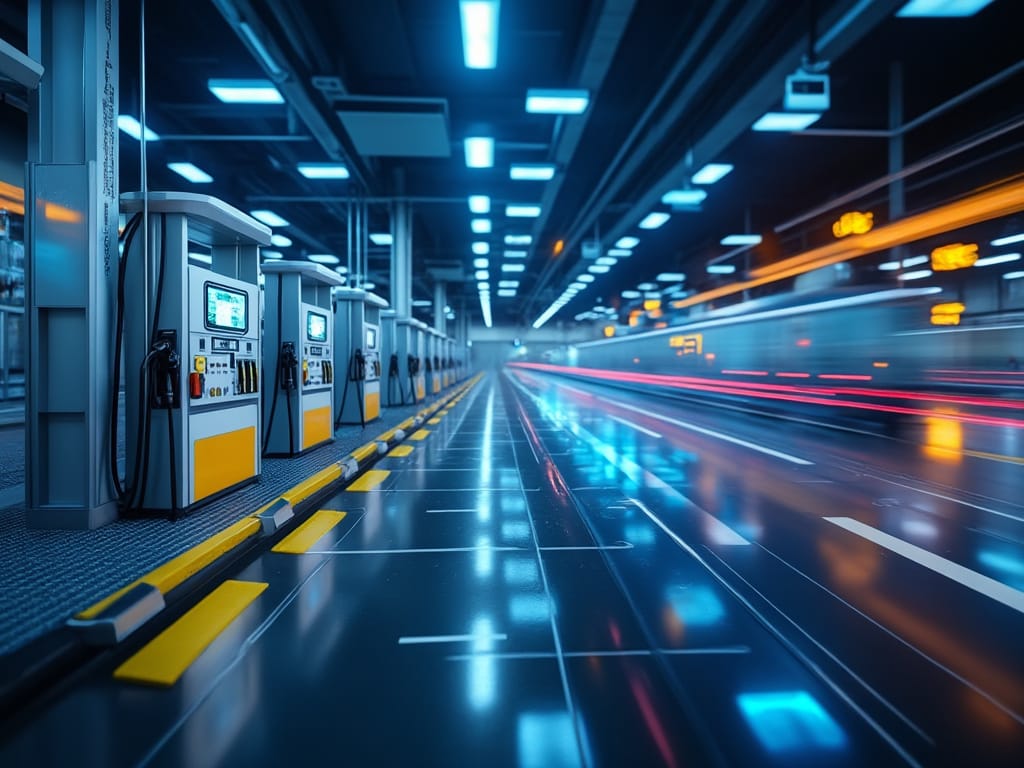
Smart Cisterns
Connected cisterns bring additional capabilities:
- Automatic Reordering: Ensure fuel supplies are always sufficient by automating reorder processes based on real-time inventory levels.
- Remote Management: Oversee multiple storage locations from a central dashboard, streamlining operations.
- Regulatory Compliance: Simplify reporting for environmental standards, ensuring adherence to regulations.
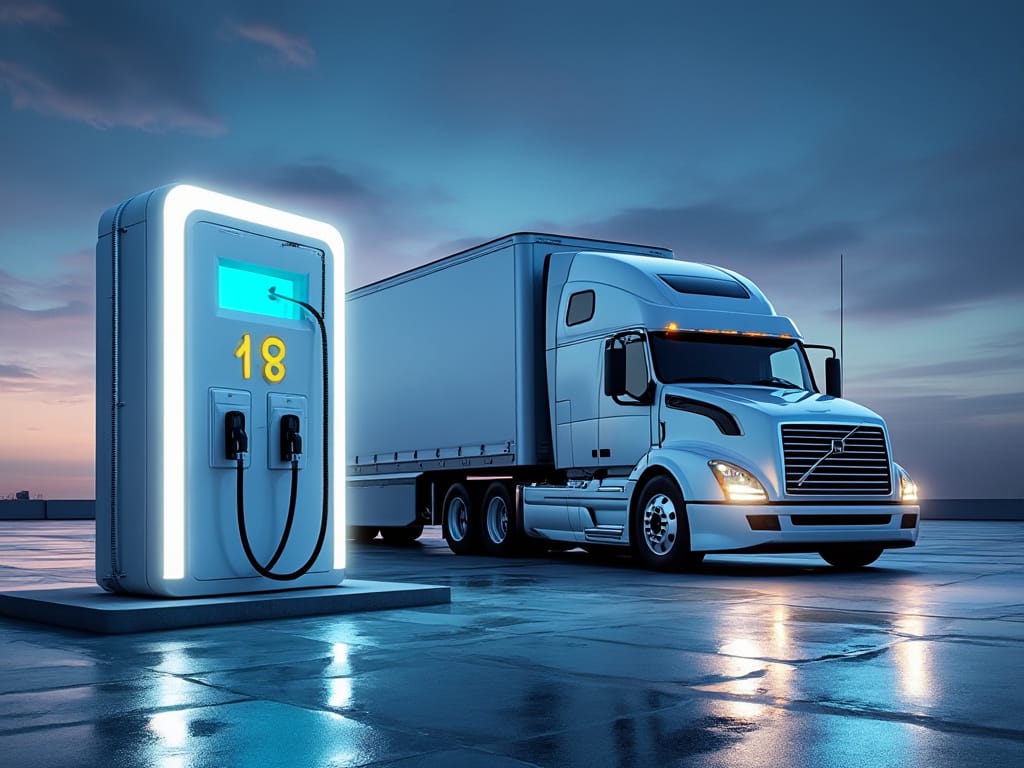
Telematics Integration
Systems like Samsara and Geotab enhance fuel tracking through telematics:
- Driver Behavior Analysis: Gain insights into driving habits that affect fuel efficiency, such as idling and acceleration patterns.
- Route Optimization: Adjust routes in real-time to reduce fuel consumption, leveraging traffic and weather data.
- Vehicle Health Monitoring: Detect maintenance needs early by monitoring engine performance and fuel usage anomalies.
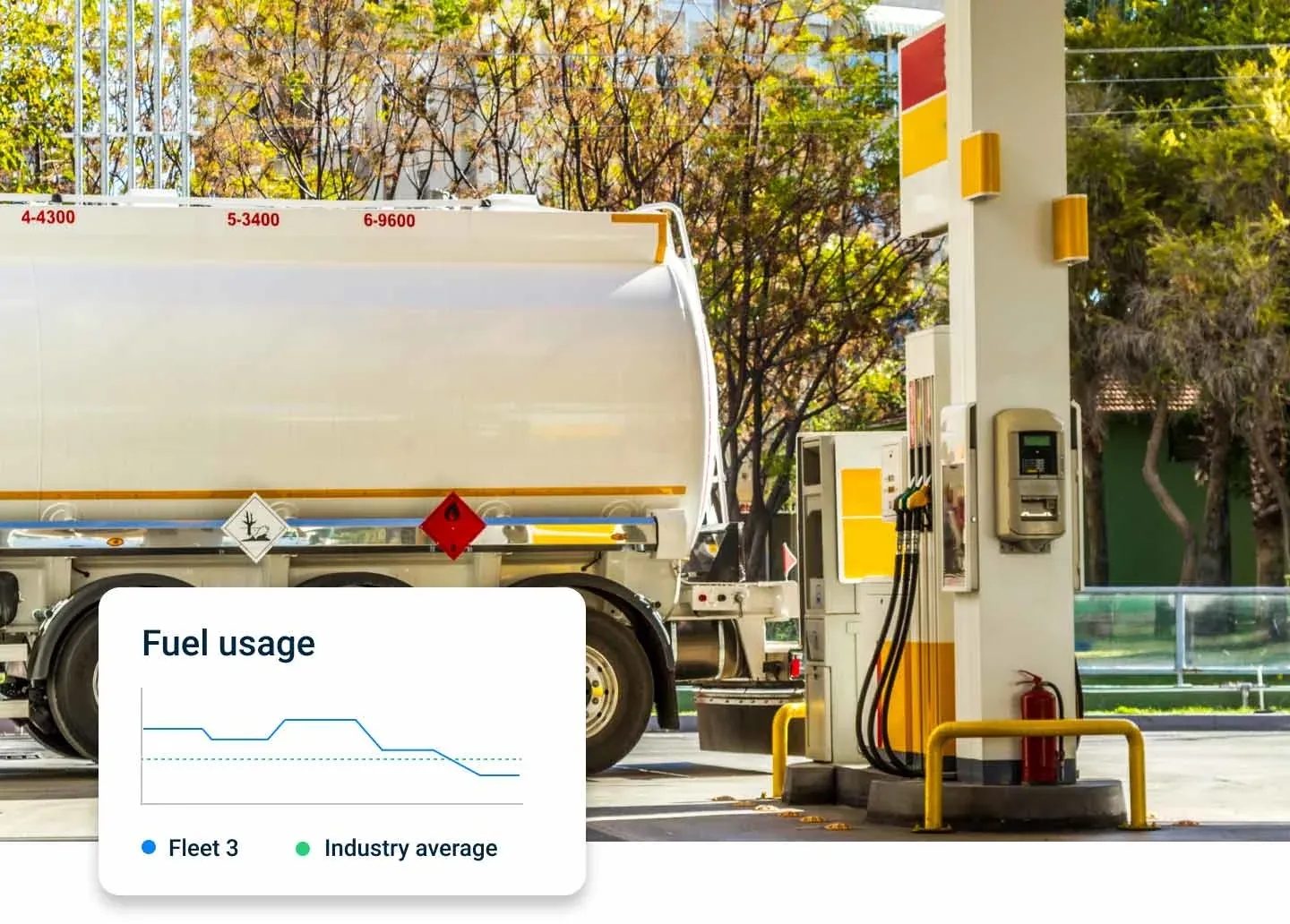
Integrating Fuel Tracking with ERP Systems
Benefits of Integration
Connecting fuel tracking data with your ERP system amplifies the advantages:
- Centralized Data Management: Achieve a unified view of operations by consolidating fuel data with other business metrics.
- Enhanced Reporting: Generate comprehensive analytics that combine multiple data sources, facilitating informed decision-making.
- Automated Workflows: Streamline processes like billing and inventory management, reducing administrative burdens.
Implementation Steps
- Data Mapping: Align fuel data fields with your ERP system to ensure seamless integration.
- API Integration: Use Application Programming Interfaces (APIs) to enable communication between fuel tracking systems and ERP platforms.
- Testing: Conduct thorough testing to verify data accuracy and system reliability before full deployment.
- Training: Provide staff with the necessary training to utilize the integrated system effectively, maximizing its benefits.
Technical Depth: Expanded API Integration Example
import requests
from requests.auth import HTTPBasicAuth
def send_fuel_data_to_erp(fuel_data):
url = "<https://your-erp-instance.com/api/fuel>"
headers = {
"Content-Type": "application/json"
}
auth = HTTPBasicAuth('your_username', 'your_password')
try:
response = requests.post(url, json=fuel_data, headers=headers, auth=auth)
response.raise_for_status()
print("Fuel data successfully sent to ERP.")
except requests.exceptions.HTTPError as err:
print(f"Error: {err}")
# Example fuel data payload
fuel_data = {
"vehicle_id": "TRK123",
"fuel_volume": 150.5,
"fuel_type": "Diesel",
"location": "Depot 5",
"timestamp": "2024-01-15T08:30:00Z"
}
send_fuel_data_to_erp(fuel_data)
Detailed templates for integrating with SAP, Odoo, and Dynamics 365 are available for download, request them by emailing us.
Tracking Fuel Consumption per Vehicle
Linking fuel data to specific vehicles provides granular insights:
- Monitoring Performance: Assess fuel efficiency on a per-vehicle basis, identifying high-consuming units.
- Identifying Inefficiencies: Spot underperforming vehicles that may require maintenance or driver retraining.
- Optimizing Operations: Tailor strategies based on consumption patterns, such as reallocating vehicles or adjusting routes.
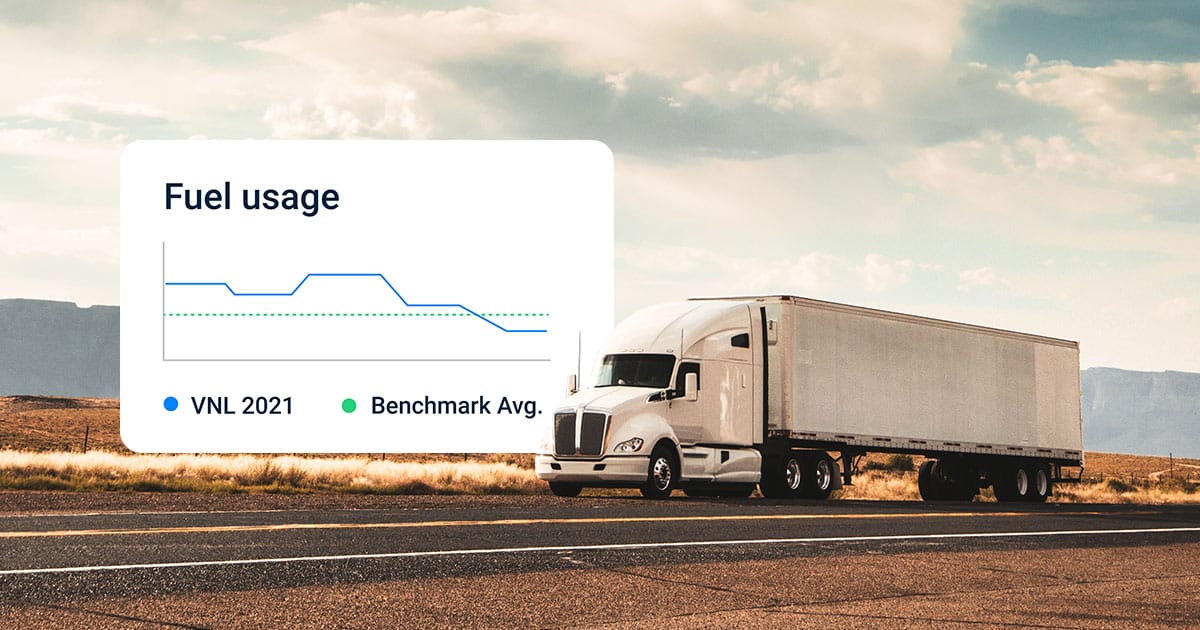
Leveraging Fuel Data for Mileage Calculations
Calculating fuel consumption relative to distance traveled enhances accuracy:
- Driver Performance Insights: Highlight areas where training can improve fuel efficiency.
- Vehicle Maintenance Indicators: Detect mechanical issues affecting consumption early on.
- Cost Allocation Accuracy: Assign fuel expenses to specific routes or clients accurately, aiding in billing and profitability analysis.
Implementing Alert Systems for Anomalies
Automated alerts for unusual fuel consumption enable proactive management:
- Early Detection: Identify issues like fuel leaks or theft quickly, minimizing losses.
- Preventive Maintenance: Schedule service for vehicles showing declining efficiency before problems escalate.
- Cost Control: Address anomalies promptly to prevent unexpected expenses.
Real-Time Vehicle Identification at the Pump
Automating vehicle identification streamlines fueling:
- Eliminates Manual Errors: Reduces data entry mistakes by automatically recognizing vehicles.
- Speeds Up Fueling: Enhances efficiency for drivers, reducing downtime.
- Ensures Accountability: Links fuel transactions directly to vehicles, improving record-keeping.
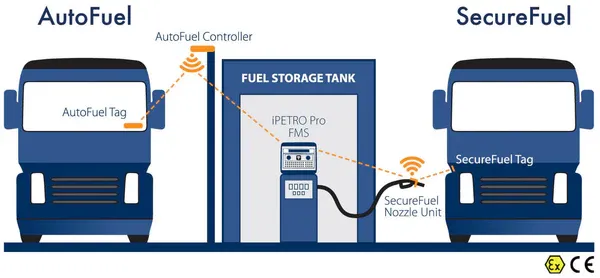
Tracking technology enhances fuel tracking accuracy and security, illustrating the process of vehicle identification at the pump.
Leading Brands in Fuel Tracking Technology
Piusi
- Specialization: Offers reliable fuel pumps and advanced management solutions.
- Features: Real-time monitoring, user-friendly interfaces, and robust security measures.
Veeder-Root
- Specialization: Provides high-precision fuel tracking with connectivity options.
- Features: Advanced tank monitoring, compliance management tools, and analytics.
OPW Fuel Management Systems
- Specialization: Focuses on automated fuel tracking and monitoring solutions.
- Features: Vehicle identification, secure access control, and comprehensive reporting capabilities.
Samsara and Geotab
- Specialization: Integrate fuel tracking with telematics for holistic fleet management.
- Features: End-to-end visibility, driver behavior analytics, and route optimization tools.
Sustainability and Cost-Savings Benefits
Environmental Impact
Implementing advanced fuel tracking contributes to sustainability efforts:
- Reduced Emissions: Optimized fuel use lowers CO₂ output, with companies reporting a 10-15% decrease in emissions.
- Regulatory Compliance: Simplifies adherence to environmental standards, avoiding fines and enhancing reputation.
- Corporate Responsibility: Demonstrates commitment to sustainability, appealing to eco-conscious clients and partners.
Financial Savings
Enhanced fuel management leads to significant cost reductions:
- Lower Fuel Costs: Directly reduce expenses by improving fuel efficiency, potentially saving 5-20% annually.
- Improved Efficiency: Increase productivity by reducing idle times and optimizing routes.
- Asset Longevity: Extend vehicle life through proactive maintenance, reducing replacement costs.
Case Studies
Case Study 1: Fuel Efficiency Improvement with Shell Fleet Solutions
Company: HOYER Group
Industry: Logistics and Bulk Liquids Transportation
Initial Challenge:
- The HOYER Group faced high fuel consumption and sought to reduce operational costs and environmental impact.
Solution Implemented:
- Partnered with Shell Fleet Solutions to implement advanced fuel management systems.
- Deployed telematics devices to monitor fuel consumption, driver behavior, and vehicle performance.
Results:
- Achieved Up to 10% Reduction in Fuel Consumption: Through optimized driving techniques and fuel management.
- Enhanced Driver Training: Data insights led to targeted driver coaching.
- Improved Environmental Impact: Reduced carbon emissions aligned with sustainability goals.
Source: Shell Fleet Solutions Case Studies
Case Study 2: Fuel Monitoring and Operational Efficiency with Microlise
Company: Wincanton
Industry: Supply Chain and Logistics Solutions
Initial Challenge:
- Wincanton aimed to improve fuel efficiency and reduce environmental impact across its fleet of over 3,400 vehicles.
Solution Implemented:
- Implemented Microlise Fleet Performance solution, providing detailed fuel usage data, driver performance metrics, and vehicle tracking.
- Integrated the system with their existing fleet management practices.
Results:
- Improved Fuel Efficiency by 10%: Through driver training and performance monitoring.
- Reduced Carbon Emissions: Contributed to sustainability targets by lowering emissions.
- Enhanced Driver Safety: Monitoring led to safer driving behaviors.
Source: Microlise Case Studies
Case Study 3: Telematics Integration with Geotab
Company: PepsiCo
Industry: Food and Beverage Distribution
Initial Challenge:
- PepsiCo sought to enhance fuel efficiency and reduce emissions across its delivery fleet.
Solution Implemented:
- Adopted Geotab's telematics platform to collect data on fuel consumption and driver behavior.
- Integrated the system with fleet management practices to optimize operations.
Results:
- Fuel Consumption Reduced by 15%: Through data-driven route optimization and driver training.
- Lowered Emissions: Significant reduction in carbon footprint contributed to sustainability initiatives.
- Enhanced Compliance: Improved record-keeping facilitated adherence to regulatory standards.
Source: Geotab Fleet Management Case Studies
Conclusion
Mastering fuel tracking is essential for logistics companies aiming to reduce costs, improve efficiency, and meet sustainability goals. By learning from industry leaders like the HOYER Group, Girteka Logistics, and PepsiCo, you can see the tangible benefits of implementing advanced fuel management systems. Integrating these technologies with your ERP and leveraging real-time data can transform your operations and lead to significant savings.
ROI Calculations and Pricing Information
Industry Benchmarks
- Average Fuel Consumption per Vehicle Type:
- Class 8 Trucks: 6.5 mpg baseline.
- Medium-Duty Trucks: 8-10 mpg baseline.
- Last-Mile Delivery Vans: 12-15 mpg baseline.
- Class 8 Trucks: 6.5 mpg baseline.
- Typical Fuel Theft Losses: Account for 3-5% of total fuel costs.
- Administrative Time Savings: Implementing automation can save 20-30 hours per month per 50 vehicles.
ROI Calculator for a 100-Vehicle Fleet
Initial Investment:
- Hardware (Pumps, Sensors): $75,000
- Software Licenses: $15,000/year
- Installation: $25,000
- Training: $10,000
- Total: $125,000
Annual Benefits:
- Fuel Savings (5%): $87,500
- Labor Savings: $36,000
- Theft Prevention: $26,250
- Maintenance Optimization: $15,000
- Total Annual Benefit: $164,750
ROI Timeline:
- Break-even: 9.1 months
- Year 1 ROI: 31.8%
- 3-Year ROI: 295.8%
Pricing Comparison Table
Solution Tier | Setup Cost | Monthly Cost/Vehicle | Features |
---|---|---|---|
Basic | $5K - $15K | $15 - $25 | Basic tracking, reporting |
Professional | $15K - $35K | $25 - $45 | ERP integration, alerts |
Enterprise | $35K+ | $45 - $75 | AI analytics, predictive insights |
Implementation Checklist
Assessment Phase (2-4 Weeks)
- [ ] Complete fleet analysis.
- [ ] Audit current systems.
- [ ] Document requirements.
- [ ] Evaluate vendors.
Setup Phase (4-8 Weeks)
- [ ] Install hardware.
- [ ] Configure software.
- [ ] Test integrations.
- [ ] Train staff.
Optimization Phase (Ongoing)
- [ ] Monitor performance weekly.
- [ ] Generate monthly efficiency reports.
- [ ] Perform quarterly system updates.
- [ ] Conduct annual ROI assessment.
Technical Details and Integration
Expanded API Integration Examples
- Use Cases: Fuel data synchronization, automated reporting, and alert notifications.
- Platforms: Integration examples for SAP, Odoo, and Dynamics 365 are provided.
Configuration Templates
- Available Templates: Pre-configured settings for major ERP systems.
- Customization Guides: Step-by-step instructions for tailoring integrations to your needs.
Security Implementation Guidelines
- Data Encryption: Employ best practices for securing data in transit and at rest.
- Access Controls: Implement role-based permissions to protect sensitive information.
- Network Security: Configure firewalls and Virtual Private Networks (VPNs) for secure connectivity.
Network Setup Instructions
- Infrastructure Requirements: Outline hardware and bandwidth considerations for optimal performance.
- Connectivity Solutions: Compare wired and wireless options based on reliability and cost.
- Redundancy Plans: Ensure system uptime through backup systems and failover mechanisms.
Future Trends in Fuel Tracking
AI and Machine Learning Integration
- Predictive Analytics: Use algorithms to anticipate maintenance needs and fuel requirements.
- Automated Decision-Making: Dynamically optimize routes and schedules based on real-time data.
Blockchain for Security
- Immutable Records: Enhance data security and transparency through decentralized ledgers.
- Smart Contracts: Automate enforcement of fuel usage policies with programmable agreements.
Regulatory Changes
- Environmental Regulations: Prepare for stricter emissions standards impacting fuel usage.
- Data Protection Laws: Adapt to increased emphasis on secure data handling and privacy.
Sustainability Initiatives
- Alternative Fuels: Integrate electric and hybrid vehicles into fuel tracking systems.
- Carbon Offsetting: Track emissions for participation in offset programs.
International Regulations and Compliance
Understanding and complying with regional regulations is crucial:
- North America: Adhere to EPA standards and state-specific regulations.
- Europe: Comply with Euro 6 emission standards and GDPR data protection laws.
- Asia-Pacific: Navigate diverse regulations across countries like China, India, and Australia.
Environmental Impact Metrics
Track and report on sustainability efforts:
- CO₂ Emissions Reduction: Monitor emissions saved through optimized fuel usage.
- Fuel Consumption Trends: Analyze long-term improvements in efficiency.
- Sustainability Reporting: Integrate fuel data into Corporate Social Responsibility (CSR) reports.
Maintenance Procedures and Troubleshooting
Routine Maintenance Schedules
- Daily Checks: Inspect fuel systems for leaks or damages.
- Weekly Tasks: Validate data integrity and apply system updates.
- Monthly Procedures: Conduct comprehensive system audits to ensure optimal performance.
Troubleshooting Decision Trees
- Connectivity Issues: Step-by-step guidance to resolve network problems.
- Data Discrepancies: Identify and correct errors in fuel data.
- Hardware Malfunctions: Diagnose and address equipment failures promptly.
Conclusion
Mastering fuel tracking is not just a technological upgrade; it's a strategic move that can transform your logistics operations. By investing in advanced fuel management systems, integrating them with your ERP, and leveraging real-time data, you position your company for significant cost savings, enhanced efficiency, and sustainable growth. The benefits are clear: optimized fuel usage, lower operational costs, and a competitive edge in the industry.
Next Steps
Unlock efficiency and savings in your logistics operations today.
- Assess Your Needs: Identify areas for improvement in fuel management.
- Consult Experts: Reach out to specialists for tailored solutions.
- Implement Technology: Choose the right tools and integrate them effectively.
- Monitor and Optimize: Continuously analyze data to refine strategies.
Contact Us
Curious about the best fuel tracking setup for your fleet? Let's talk!
- Email: mehdi@miragemetrics.com
- Website: www.miragemetrics.com
- Schedule a Free Call: Book a Consultation
References
- Piusi: www.piusi.com
- Veeder-Root: www.veeder.com
- OPW Fuel Management Systems: www.opwglobal.com
- Samsara: www.samsara.com
- Geotab: www.geotab.com
- Logistics Management Journal: Fuel Management in Logistics, 2023
- Environmental Transport Association: Sustainability in Trucking, 2022
- EPA Regulations: www.epa.gov
- EU Emission Standards: www.europa.eu
- International Energy Agency Reports: Global Fuel Regulations
Mirage Metrics
AI-powered solutions for logistics and supply chain optimization, enhancing efficiency and real-time decision-making.
Call to Action
Ready to transform your fuel management strategy? Schedule a free consultation with Mirage Metrics today.
Client Testimonials
"Implementing advanced fuel tracking with Mirage Metrics reduced our fuel costs by 5% within the first year. Their expertise made the integration seamless."
— Yassine B., CEO at Transwin
Expert Quote
"Investing in fuel tracking technology is no longer optional for logistics companies aiming to stay competitive. It's a strategic move that delivers substantial ROI and supports sustainability goals."
— Michael K., Industry Analyst at Logistics Insight
Stay ahead of the curve by embracing the latest in fuel tracking technology. Transform your logistics operations with Mirage Metrics.